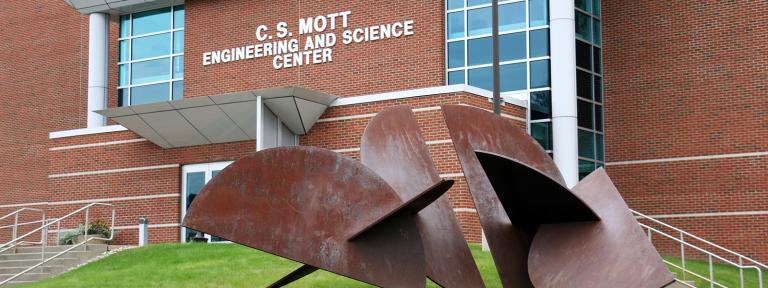
“Waste not, want not.” Grandma’s advice is still good today. General Dynamics is trying to heed that advice by working with Kettering researchers to identify the most efficient strategies for harvesting wasted heat energy in propulsion systems.
Approximately one third of the heat produced from combustion in an internal combustion (IC) engine is converted into mechanical energy. The other two thirds are lost through the cooling and exhaust systems. Utilizing this wasted heat could improve fuel economy in automobiles and reduce energy consumption in IC engines.
Dr. Bassem Ramadan, professor of Mechanical Engineering and Dr. Yaomin Dong, assistant professor of Mechanical Engineering, are working on the General Dynamics research. Ramadan and Dong’s role is to review existing waste energy recovery technologies and to perform mathematical modeling and computer analysis of waste heat recovery systems.
“They are specifically interested in land vehicles that use a lot of energy,” Ramadan said. General Dynamics wants to determine whether:
Electricity can be generated from engine waste heat using a thermoelectric device;
If it is feasible to use a heat exchanger to generate steam which would power a steam turbine that could be coupled to a crankshaft;
If waste heat can be used to run a Stirling engine (external combustion engine); and
Can waste heat be applied to absorption refrigeration systems?
For Phase One, Dong and Ramadan focused on the thermoelectric device because it does not require complex machinery. “It is a simple device that has no moving parts and requires no maintenance,” he said. “We are already seeing some promising results.”
A thermoelectric device converts thermal energy into electricity. By applying a temperature difference across the thermoelectric device, an electric voltage is induced. The higher the temperature difference applied across the material, the higher the voltage.
“The electricity generated by a thermoelectric system could be used to power other electrical systems in the vehicle or to charge a battery,” said Ramadan, “allowing alternators to work less, draining the battery less, and also requiring a smaller cooling system.”
“Currently thermoelectric devices have a low efficiency,” he said, “but with new materials research, it is shown they can achieve significantly higher efficiencies.”
If the new materials can improve efficiencies, they could potentially be used in a variety of applications from vehicles to furnaces and generators – anything that gets hot, Ramadan said. In passive use applications it could even be used in homes to generate electrical energy, Ramadan added.
In Phase Two of the Kettering research for General Dynamics, Ramadan and Dong will put these thermoelectric generators to the test – literally – by moving from the computer simulations to the lab.
The proposed Phase Two involves developing a test stand to characterize a thermoelectric generator (TEG) using exhaust gases which will be used as the heat input, building a heat exchanger to allow the transfer of heat from the hot gases to one side of the thermoelectric device and from another side to a heat sink, and testing the performance of the thermoelectric generator under realistic operating conditions.
Their goal is to determine the controlling parameters and optimize the design of the TEG including size, weight, location, and electrical interfaces for future testing in a vehicle outside of laboratory conditions.
Written by Dawn Hibbard
810.762.9865
dhibbard@kettering.edu