News & Events

Latest News
2024 Kettering Magazine
2024 Kettering Magazine
Read how Kettering graduates, groundbreaking research, and strategic partnerships are shaping the future in the Kettering University 2024 Magazine.
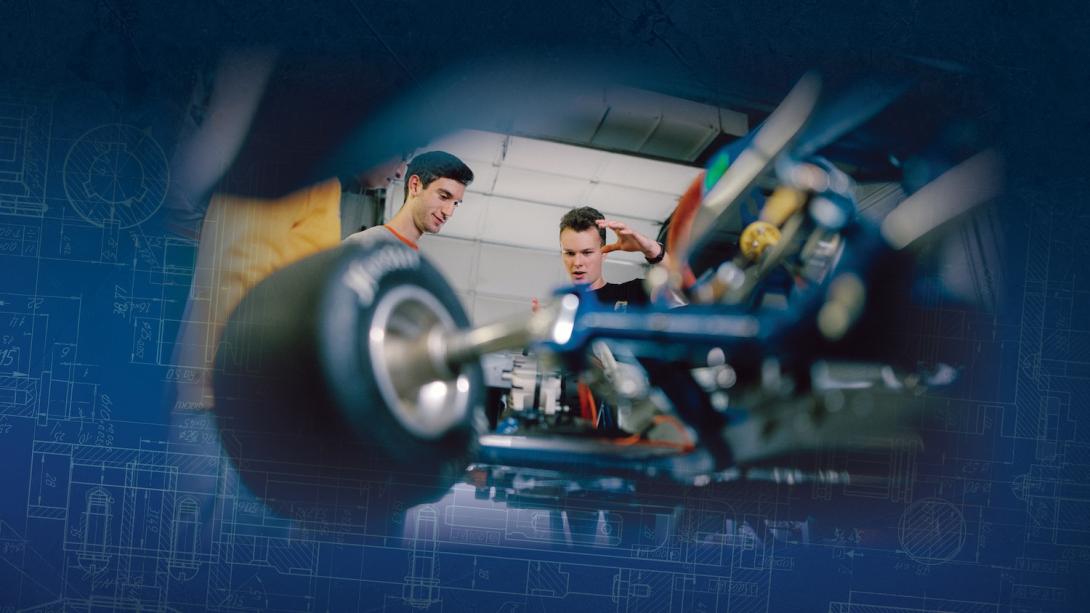
Horsepower to Hyperloops Podcast
Horsepower to Hyperloops Podcast
Learn about groundbreaking ideas, noteworthy advancements and the latest developments in mobility, technology, medicine and many other fields.
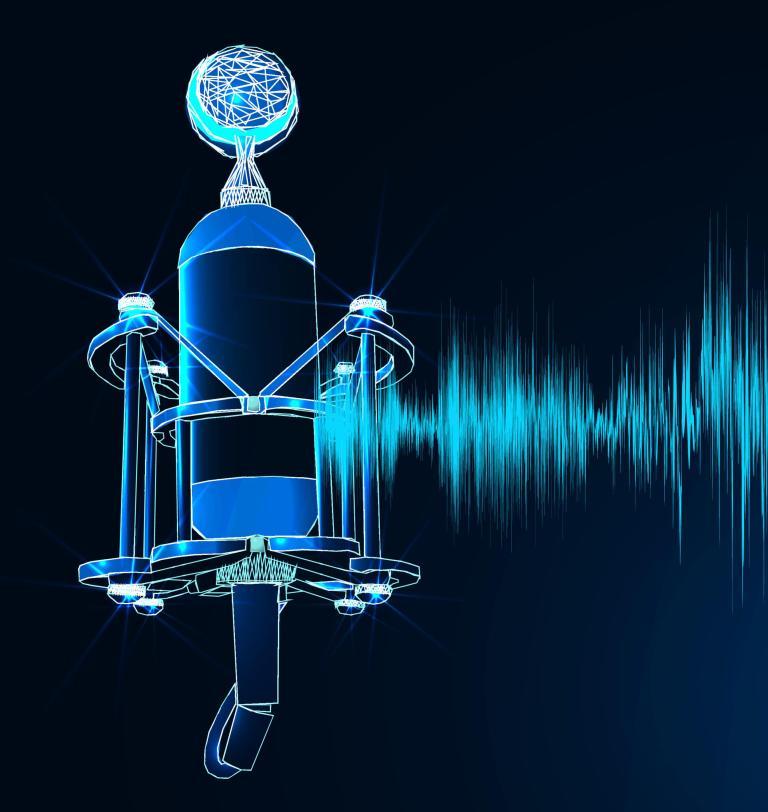
Campus News Brief
Lorem ipsum dolor sit amet, consectetur adipiscing elit, sed do eiusmod tempor incididunt ut labore et dolore magna aliqua. Ut enim ad minim veniam.
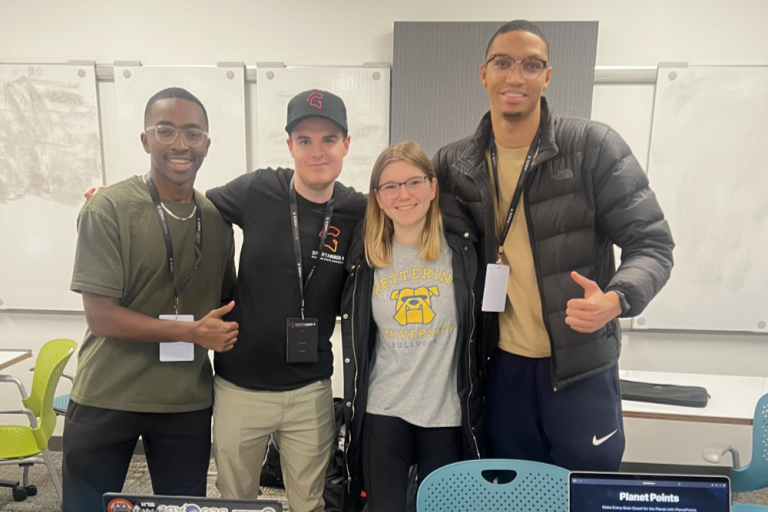
Kettering Students Awarded at Michigan State University's SpartaHack 9
Amanda Koziol, Jaydin Freeman and David Glover won the Sustainability-Climate Change Mitigation Hack and the MSUFCU-Community Class Act Hack at Michigan State University's ninth annual student-run hackathon, SpartaHack 9.
Over 600 student developers and designers gathered at Michigan State University in East Lansing on January 27th, 2024, with a unifying challenge: engineer innovative solutions to everyday problems - in just 24 hours.
Hackers had to make their projects track-specific and pitch them to judges, who used criteria including uniqueness, technical implementation, and practicality.
Their projects can be found below:
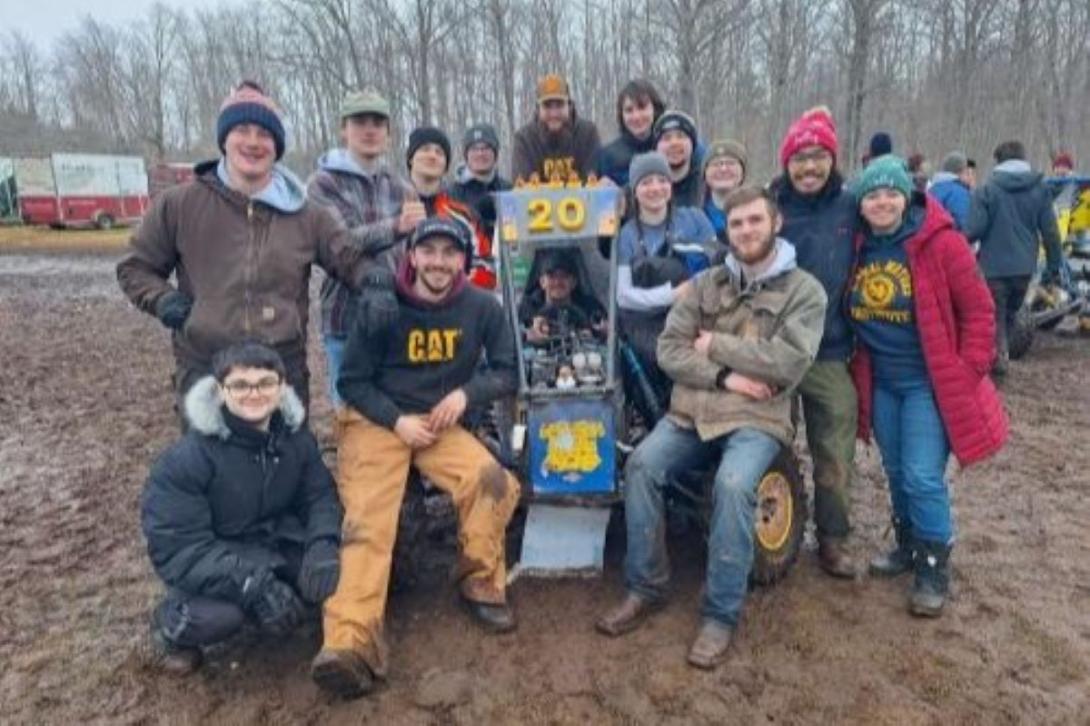
Baja SAE Team Excell at '24 Winter Baja Competition
Kettering's Baja SAE team competed in the Winter Baja Competition on January 27, 2024 in Houghton, MI. They brought home 2nd place in the Hill Climb and Pickled Egg Slalom and 23rd in the endurance race.
"We were able to get new drivers some drive time in a competitive environment. We learned a lot, and it was a great experience overall."
- Jake Dancel, Team Lead and Electronics Lead for Kettering Baja SAE
Interested in being part of the Baja team's journey? The team meets every Wednesday at 7 p.m. in Room 1221 at the C.S. Mott Engineering and Science Center.
All Kettering students are welcome to join!
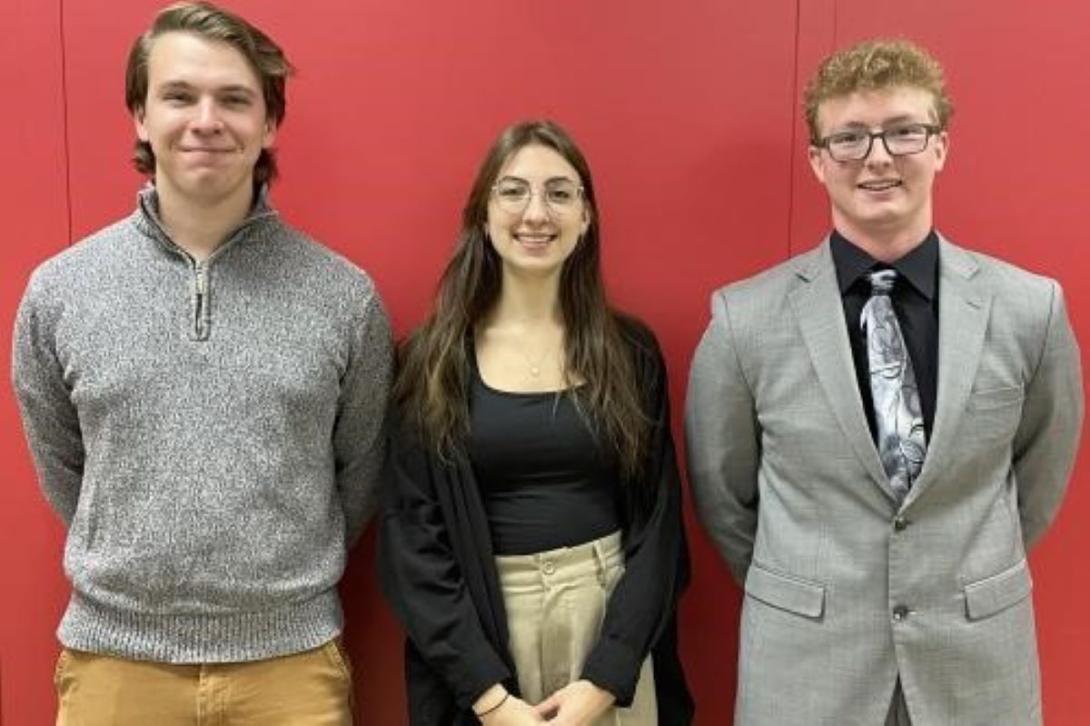
Tau Beta Pi Initiates New Members
Tau Beta Pi initiated three new members Dec. 13.
Tau Beta Pi is an engineering honor society. To be eligible for membership, undergraduate students must be in the top 12.5% of their junior class or the top 20% of their senior class and exhibit exemplary character.
Congratulations to Alexander Moening ('24, ME), Magdalena Sawicki ('24, IE) and Colin Stewart ('24, ME).
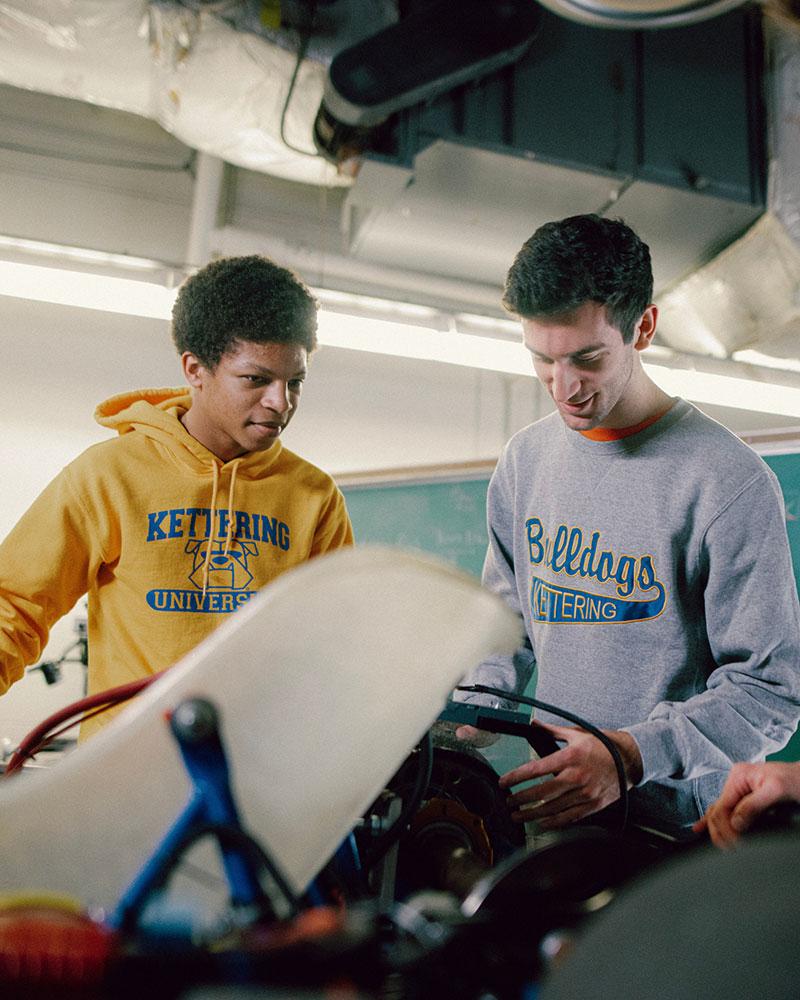
Eta Kappa Nu Initiates New Members
The Theta Epsilon chapter of Eta Kappa Nu, the Electrical and Computer Engineering honor society, initiated three new members Dec. 7.
To qualify for membership, students must be in the top 25% of their junior class or top 33% of their senior class and exhibit positive character traits.
Congratulations to Doug Ray ('25, EE), Jack Sigelko ('25, CE) and Nick Young ('24, EE).